
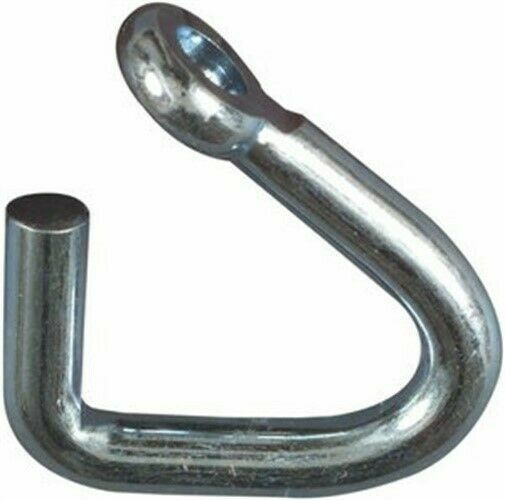
The following will provide a comprehensive overview of the metal forging process. It is important to understand the principles of manufacturing forged products, including different techniques and basic metal forging design. Aluminum, magnesium, copper, titanium, and nickel alloys are also commonly forged metals. Various tests are described latter to determine forging process factors for different materials. Different types of metals will have a different factors involved when forging them, some will be easier to forge than others. Metal forging is known to produce some of the strongest manufactured parts compared to other metal manufacturing processes, and obviously, is not just limited to iron and steel forging but to other metals as well. These material properties are often greatly improved. The forge will then manufacture steel forgings of desired geometry and specific material properties. Work stock is input to the forge, it may be rolled, it may also come directly from cast ingots or continuous castings. A steel forge is often a source of great output and productivity. The forging process is very important in industrial metal manufacture, particularly in the extensive iron and steel manufacturing industry. Metal forging is a metal forming process that involves applying compressive forces to a work piece to deform it, and create a desired geometric change to the material. Lubrication In Industrial Metal Forging Manufacture Classification Of Metal Forging Processes
